Social
효성그룹의 안전보건
효성은 안전보건을 기업활동의 최우선 가치로 인식하고 있습니다.
임직원, 고객, 협력사, 도급사, 지역사회 등 다양한 이해관계자를 위한 안전하고 건강한 일터를 만들기 위해 최선을 다하고 있습니다. 또한, 높아지는
안전보건에 대한 사회적 요구 수준에 대응할 수 있도록, 국내 및 국제기준에 부합한 안전보건경영체계를 갖추고 있습니다.
효성은 지속적인 안전보건 개선과 예방활동을 추진합니다.
안전보건경영방침 및 추진전략에 따라 세부 실행과제를 수립, 정기적으로 평가하고, 책임감 있는 자세로 안전보건 비전을 달성하고자 합니다. 또한, 교육 훈련을 통한 안전보건 의식 제고, 위험성 평가를 통한 중대 위험 발굴 및 개선, 실천 중심의 안전보건 문화 정착에 집중하고 있습니다.
안전보건환경 경영방침
Link Copy당사는 안전보건환경 방침을 성실히 준수하여 무재해 사업장 구현과 사회적 책임을 다하고, 고객과 함께 성장하는 기업으로 도약하기 위해서 지속적으로 노력하며 전 임직원은 이를 숙지하고 내 외부의 이해관계자들이 알 수 있도록 한다.
안전보건환경 경영방침 포스터
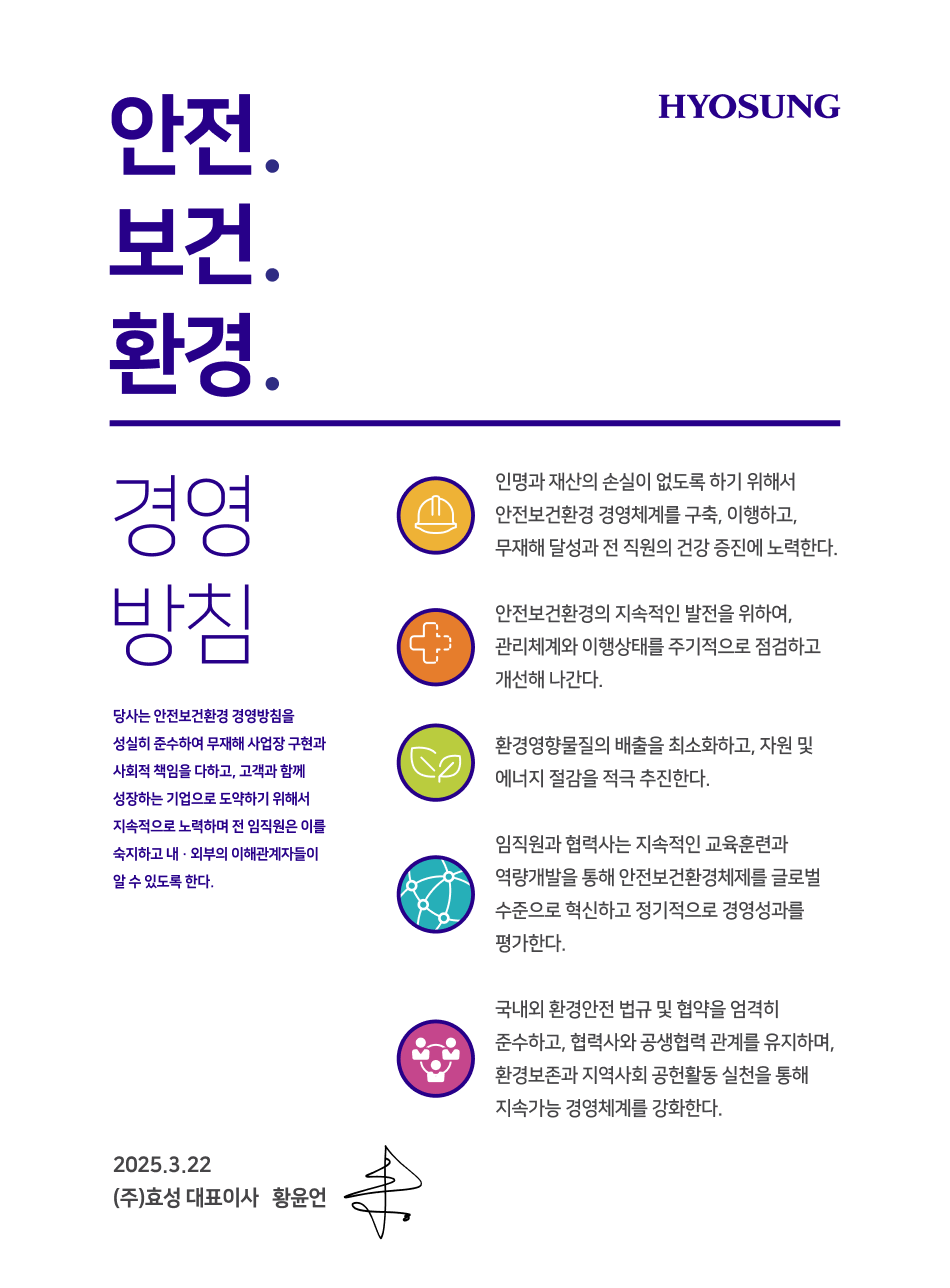
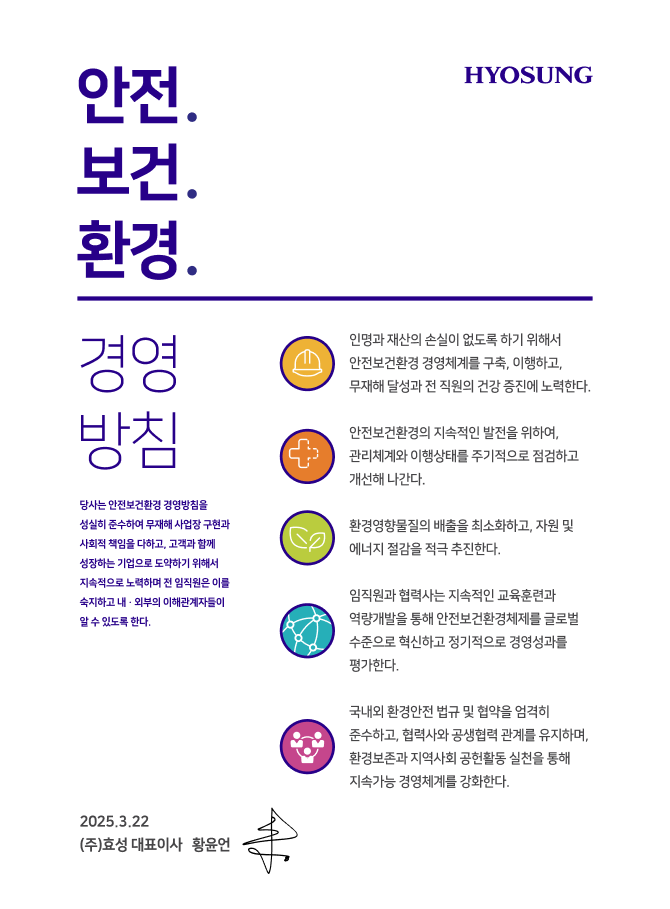
안전보건 경영체계
Link Copy㈜효성은 임직원과 이해관계자의 안전을 최우선 가치로 삼고, 체계적인 안전보건 경영을 실천하고 있습니다. 조직 전반의 관리 체계를 기반으로, 안전보건 비전과 실행 전략을 수립하고 있으며, 2030년까지의 중장기 로드맵을 통해 산업재해 예방과 안전문화 확산을 지속적으로 추진하고 있습니다. 이를 통해 효성은 지속 가능한 경영환경을 조성하고, 모두가 안심할 수 있는 일터를 만들어가고자 합니다.
안전보건 조직체계
㈜효성은 이사회 산하의 ESG경영위원회와 대표이사 산하의 ESG경영 추진위원회를 통해 안전보건 관련 현황과 주요 리스크를 관리·감독하고 있습니다. CSO(안전 최고책임자)는 ESG경영 추진위원회에 안전보건 경영 현황과 이슈를 정기적으로 보고하며, 안전보건팀은 전 사업장의 안전보건 관리체계를 총괄합니다.
각 사업장에는 안전보건 총괄 책임자를 선임하여 산업재해 예방계획 수립 및 실행을 주도하고 있으며, 안양공장, 기술원, 중공업연구소 등은 환경안전팀을 별도로 운영하여 안전, 보건, 환경, 소방을 전담하고 있습니다.
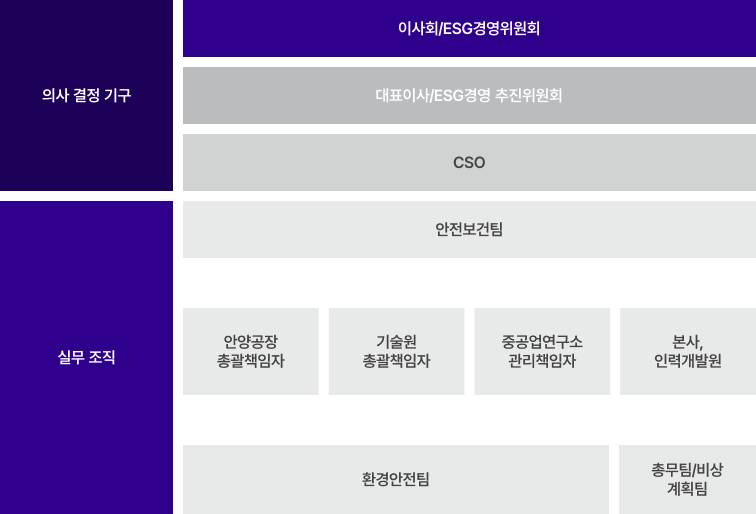
- 이사회/ESG경영위원회
- 대표이사/ESG경영 추진위원회
- CSO
총괄책임자
총괄책임자
관리책임자
인력개발원
계획팀
안전보건 비전 및 추진전략
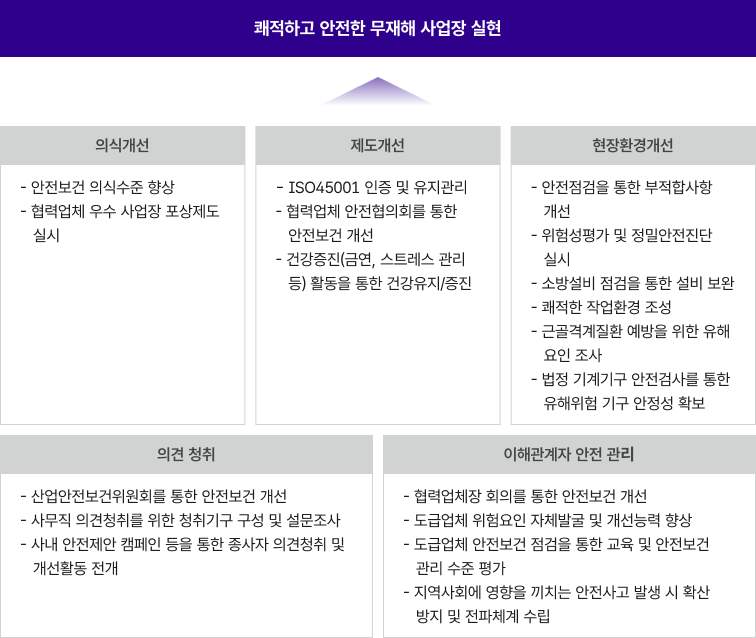
- 의식개선
-
안전보건 의식수준 향상
협력업체 우수 사업장 포상제도 실시
- 제도개선
-
ISO45001 인증 및 유지관리
협력업체 안전협의회를 통한 안전보건 개선
건강증진(금연, 스트레스 관리 등) 활동을 통한 건강유지/증진
- 현장환경개선
-
안전점검을 통한 부적합사항 개선
위험성평가 및 정밀안전진단 실시
소방설비 점검을 통한 설비 보완
쾌적한 작업환경 조성
근골격계질환 예방을 위한 유해 요인 조사
법정 기계기구 안전검사를 통한 유해위험 기구 안정성 확보
- 의견 청취
-
산업안전보건위원회를 통한 안전보건 개선
사무직 의견청취를 위한 청취기구 구성 및 설문조사
사내 안전제안 캠페인 등을 통한 종사자 의견청취 및 개선활동 전개
- 이해관계자 안전 관리
-
협력업체장 회의를 통한 안전보건 개선
도급업체 위험요인 자체발굴 및 개선능력 향상
도급업체 안전보건 점검을 통한 교육 및 안전보건 관리 수준 평가
지역사회에 영향을 끼치는 안전사고 발생 시 확산 방지 및 전파체계 수립
안전보건 2030 로드맵
중장기 목표 | 2023 안전보건관리체계 구축 | ~2026 자기규율예방체계 구축 | ~2028 자기규율예방체계 내실화 | ~2030 Global 수준 안전보건 경영시스템달성 |
---|---|---|---|---|
핵심 과제 |
관련 법령, 법규 규정 정비 및 준수 안전보건시스템 인증 유지관리(ISO 45001) 사업장 무재해 운동 추진 중대재해 고위험 설비 집중 관리 |
위험성평가 운영시스템 확립 사내 협력사의 안전보건 관리 체계 구축 지원을 통한 상생 협력 강화 안전문화 캠페인을 통한 종사자 참여 확대 비상상황 대응 훈련 강화 및 응급 의료 대응체계 정비 |
현장 중심 교육을 통한 위험성 평가 실행력 제고 전문기관 교육을 통한 관리 감독자 역량 향상 참여와 협력을 통한 안전 의식 제고 및 문화확산 |
Global 사업장 안전관리 체계 구축 및 관리 강화 사외 협력사의 안전보건 관리 체계 구축 지원을 통한 상생 협력 강화 종사자 전원의 자발적 참여를 통한 Global 수준의 안전문화 정착 |
LTIFR | 0.0 | 0.0 | 0.0 | 0.0 |
LTIFR(Lost Time Injury Frequency Rate) = 산재 건 수*1,000,000/ 총 근로자 근무시간(100만 근로시간 당 휴업 재해 발생 건수)
안전보건 활동
Link Copy안전보건 이행사항 점검
㈜효성은 안전보건 경영방침을 바탕으로 무재해 작업장 구현을 목표로 하고 있습니다. 사업장별로 의식과 제도, 현장 환경 개선, 의견 청취, 이해관계자 안전관리를 위한 실행과제를 수립하고 분기별로 모니터링을 실시하여 이행사항을 점검하고 있습니다.
안양사업장 정기 안전점검
㈜효성은 안양사업장(안양공장, 기술원, 중공업연구소)의 안전점검을 강화하기 위하여 일상점검/테마점검/노사합동 안전보건점검/도급업체 안전보건점검을 실시하고 있습니다. 또한, 정기 안전점검 및 화재예방 특별점검을 수행하고 도출된 부적합 항목에 대해 개선 조치를 이행하고 있습니다.
점검명 | 점검자 | 점검주기 | 점검내용 | 비고 |
---|---|---|---|---|
일상점검 | 팀장, 안전관리자 | 매일 |
총 185 건 Check Sheet를 운영 중이며, 연 2회 정기 개정토록 강화 안전관리 실무 담당자 소속부서와 안전보건 팀 관리감독 기능 강화 |
빈공간 |
테마점검 | 안전보건관리 (총괄) 책임자,팀장, 환경안전팀 | 매월 |
사전 점검항목을 수립하고, Patrol 시에는 대상항목을 전수점검 안전보건팀은 안양공장, 기술원, 중공업연구소 점검 시 이행실적을 관리감독 |
대표이사보고 (월 1회) |
노사합동 안전보건점검 | 협의회 구성원 | 매분기 |
기존 노조 및 근로자 대표 요구사항, 건의함, 설문조사의 개선조치 사항을 포함하여 점검 |
대표이사보고 (반기 1회) |
도급업체 안전보건점검 | 안전관리자, 도급업체장 | 매월 |
도급업체장 회의 시, 건의된 사항에 대한 합동 점검(월 1회) 도급업체별 안전관리실태 평가(분기 1회) 및 보고(반기 1회) |
대표이사보고 (반기 1회) |
사업장별 주요 점검 내용
타이틀 | 내용 |
---|---|
안양공장 | 안전점검 및 위험물 누출 점검 |
기술원 | 61개 실험실 및 일상점검표, 비상연락망, 소화기 점검표, 산업안전보건 게시판 점검 |
중공업연구소 | 71개소 화재예방 시설(소화기 67개소, 소화전 4개소) 점검 |
위험성 평가 실시
㈜효성은 매년 관리감독자와 근로자 참여하에 위험성평가를 실시하여, 안전관리가 미흡한 사항을 발굴하고 안전관리계획서에 반영하고 있습니다. 사업장 각 팀별 자체 위험성 평가를 실시하여 개선대책 수립 후, 계획 일정 내 조치를 진행하고 있으며, 개선실적 및 효과성은 월 1회 보고하고 있습니다. 또한, 당사 및 타사의 사고사례를 전 공장에 공유하여 유사 사고 위험이 있는 작업의 경우 선제적인 예방계획을 수립하고 있습니다.
안전보건소식지 발간
㈜효성은 환경안전보건(EHS) 의식 향상을 위하여 소식지를 발간하고, 월례조회 시 안전보건관리책임자의 당부 사항을 발표하고 있습니다. 이와 더불어 임원회의 시 안전보건 이슈사항을 정기적으로 공유하고, 안전보건 준수사항과 비상사태 시 대피 요령을 담은 팸플릿을 제공하고 있습니다.
안전우선작업권 제도 운영
효성은 안전우선작업권 제도를 운영하여 작업 중 위험 발생 시 근로자의 작업 중단과 함께 즉시 대피하여 안전 조치를 확인한 후 작업을 재개하고 있습니다.
건강증진 제도
효성은 임직원 및 협력사 직원의 건강증진을 위해 각 사업회사별로 다양한 건강증진 제도를 운영하고 있습니다. 매년 전사 임직원을 대상으로 건강검진을 실시하고 있으며, 임직원의 건강관리와 유소견자 추적관리를 위해 산업간호사가 관리하는 건강관리실을 운영하여 임직원 건강증진을 위한 환경을 제공하고 있습니다. 또한 근골격 질환, 청력보존, 뇌심혈관 질환 예방 프로그램을 운영하고 있으며 비만, 금연, 근골격 질환으로 구성된 건강펀드를 통해 임직원 및 협력사 직원의 안전과 건강을 확보하고 있습니다.
제도 | 주요 내용 |
---|---|
건강증진 프로그램 |
뇌심혈관 질환 예방 프로그램 비만, 금연, 근골격 질환 관련 건강펀드 운영 |
근로자 건강검진 |
건강관리실 운영 특수/임시/수시 건강진단 |
작업환경 관리 |
근골격계 질환 관리 프로그램 밀폐공간 작업 관리 프로그램 청력보존 프로그램 |
감염 예방 활동 |
감염병 행동지침 마련 및 전사 공지 실시간 COVID-19 상황 SNS 알림 사내 출입자 대상 비접촉식 체온 측정 비대면 업무 방식 활용 |
제도별 상세내용은 사업회사별로 일부 다를 수 있습니다.